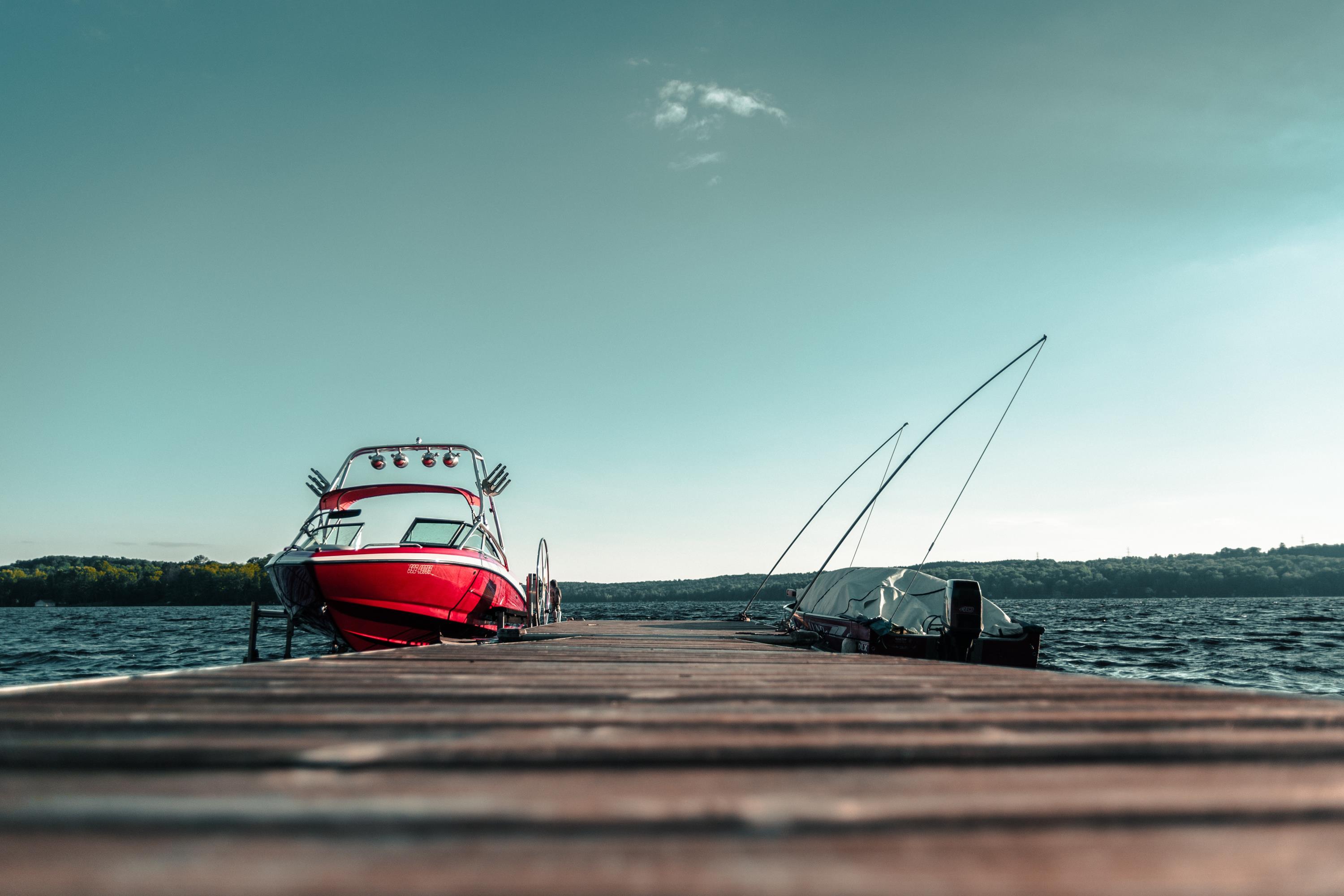
Choosing The Right Repair Facility
Based on an article by Charles Fort for BoatUS
Your local boatyard and marina want your unwavering customer loyalty. Here's how to pick a professional outfit that delivers all the service you expect.
No matter how well we maintain our boats, from time to time they need repairs and servicing, which means that if you don't already have one, eventually you're going to need to find a good, reliable shop. A top-flight shop can make your boating life much easier and less stressful, but how do you find one?
First Impressions Are Important
Good shop: A clean and organized facility reveals a lot. A shop that looks orderly and neat shows that management and employees care about their workplace as well as about details, which usually leads to caring about their customers.
Bad shop: A messy shop floor or waiting area doesn't always mean sloppy work. But if workers can't keep the service counter organized, how can you be sure they keep their parts ordering or invoices accurate? A bunch of boats randomly scattered and left uncovered in the parking lot isn't a good sign, either.
Communication Is Critical
Good shop: A good facility will answer the phone, return promised calls, and be willing to address your concerns and explain something you might not understand. Boat repairs can be complicated, so when a problem crops up, a good facility will call you before proceeding. And the employees will be professional and polite, and welcome your concerns.
Bad shop: There's nothing worse than an unanswered phone — unless it's an unreturned call. Shops that don't call back may simply be booked up and busy doing good work, but they also may be stalling for time or avoiding the fact that they haven't even begun your job. If you can't get hold of the shop before you bring your boat in, you may have problems getting questions answered or someone to address a problem later. If you bring in your outboard for a simple tune-up, it's better to hear right away that they've found a problem with the fuel system rather then later, when you come to pick it up.
Training + Certifications = Better Service
Good shop: Facilities that have factory-trained technicians demonstrate that management is serious about quality. If you have a MerCruiser engine, you can expect better repairs from a tech who has been to MerCruiser training. Ask the shop if workers are trained on the type of engine or boat you're bringing in for repair. The American Boat & Yacht Council (ABYC) certifies technicians to make repairs to ABYC standards. ABYC Master Technicians have completed courses and know how to apply thos standards. A business that is proud of its technicians will often display their pictures in the shop or on its website along with their credentials. Training costs money, and well-trained techs demand better wages, so expect to pay a little more.
Bad shop: There are plenty of talented technicians who've learned on the job. But with complicated electronic controls and a constant stream of new products, training is not optional. Especially if you have an engine that's under warranty, ask for a factory-trained tech for maintenance.
Follow The Paper Trail
Good shop: When you drop off your boat, expect an accurate work order (the initial paperwork describing what's wrong) with a realistic estimate. The nature of boats means that sometimes repairs on one thing will reveal further problems somewhere else. An estimate is just that, but a good shop will have realistic knowledge of how long most repairs take. When completed, a repair job includes a comprehensive invoice (final bill) detailing all labor, parts, and miscellaneous charges.
Bad shop: BoatUS Consumer Protection has seen many complaints with work orders that say nothing more than "fix engine." Such an open-ended work order is bound to end up with a repair that's more complicated and an invoice that's more expensive then you expect. When it's time for the invoice, a shop that simply says "engine fixed" leaves owners wondering what the repair was and if it even took place. Beware of a shop that demands upfront payment or only takes cash — it may not be around for long.
Warranty Work
Good shop: A repair facility that's proud of its work will stand behind it with a written warranty. Three to six months is a reasonable time to ensure the repair worked; more is better. Parts and labor are often covered by different warranties, which should be made clear on the invoice.
Bad shop: "Don't worry. We'll take care of any problems" is not a warranty. The legal adage, "If it's not in writing, it didn't happen" applies here. Without a written warranty, a verbal assurance means the warranty — if there is one — is whatever the shop wants.
Do An Online Search
Good shop: Internet reviews make it easier to find shops that do quality work. Online review sites such as Yelp and Google can be helpful in choosing a repair facility. But look carefully — a single dissatisfied customer can carpet the internet with negative reviews. Look also at the reviewers' names. Real names carry more weight than fastboatguy98. Shops with several good reviews that go back a few years are a better bet.
A certified Clean Marina can be another sign of a "good shop." If these marinas are taking care of the environment, chances are they will also take good care of you.
Anyone can throw up a website, and many shops do just that with whichever volunteer is willing to step up. But a shop that goes the extra mile by including short articles or blogs about relevant topics, as well as matters such as hours, emergency numbers, and specials — and keeps it up to date — shows it understands what people expect today. An online mission statement is a plus, too. When there's a problem, you can sometimes make progress by asking if the manager of the shop is following its published mission statement.
Bad shop: If an online search returns a barrage of complaints from several different sources, there's usually a reason. Most people are not shy about giving their opinions online, especially when they're negative. Keep in mind, though, that reviews typically have an unlimited life span, so if the negative ones are old and new ones are glowing, it may be a sign of new (better) ownership or management.
A missing website doesn't automatically mean bad service — it could just be a busy shop. But it could also be a sign of a very new shop or ownership that's not current or comfortable enough with technology — not something you want for your complicated electronics.
Consumer-Protection Alert
You might assume that when your boat or engine is in the dealer's shop for routine maintenance or repair, your technician will automatically check for any service bulletins or recalls issued. The truth is that the shop probably will not check for this information automatically. Ask the shop specifically to check the computer system for bulletins or recalls that may affect your boat. Keep in mind that the cost involved in correcting a safety recall issued by the manufacturer or the U.S. Coast Guard (USCG) is usually absorbed by the manufacturer. But any costs associated with a service bulletin are usually the boat owner's responsibility.
You can also check the USCG database for recalls yourself. They're posted on the USCG website.